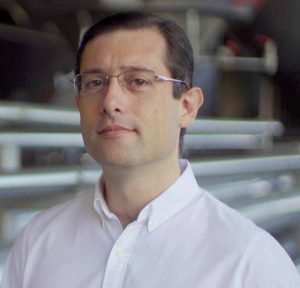
Alaercio Nicoletti Junior, Qualidade e
Melhoria Contínua – CORP. – Grupo Petrópolis
“Nada se compara à eficácia do Seis Sigma na hora de melhorar a eficiência operacional da empresa, aumentando a produtividade e reduzindo custos. Aprimora os processos de projetos, acelera a velocidade de lançamento de produtos, com menos defeitos, e reforça a lealdade dos clientes.Talvez o maior, mas menos alardeado benefício do Seis Sigma seja a capacidade de desenvolver um quadro de grandes líderes.” Jack Welch
O Seis Sigma foi destaque nas grandes empresas desde sua origem, na Motorola (1987), até o final da década de 90, passando por um boom mundial quando apadrinhado por Jack Welch, CEO da General Electric (GE). Mesmo usando ferramentas estatísticas clássicas, como o conceito de normalidade, média e desvio padrão desenvolvidos a partir do século XIX, vestiu-se de um manto nobre, pois, continha algo mais que simples ferramentas dispersas. O segredo do Seis Sigma era sua estruturação em um método científico, sob a forma do DMAIC (Define, Measure, Analyze, Improve e Control), como é mais conhecido, ou do próprio PDCA (Plan, Do, Check, Act) de Shewart e Deming.
Num caminho paralelo consolidou-se o Lean Thinking, originado na década de 50 no Japão, e caracterizado pela forma simples e eficaz com que reduzia os desperdícios organizacionais com técnicas que contavam com desenvolvimento de pessoas com os sentidos aguçados para a identificação de oportunidades e o uso de bom senso para as soluções. Mais que o método, o Lean valoriza a disciplina do kaizen, rápido e focado, atuando assim como o Seis Sigma nos processos.
No final da década de 90, por influência inicial da indústria automotiva que buscava no Sistema Toyota de Produção (ou Lean Manufacturing) formas de melhorar sua flexibilidade de produção, produtividade e qualidade, surgiu a inevitável parceria entre o Seis Sigma e o Pensamento Enxuto (Lean Thinking), originando o que se chamou de Lean Seis Sigma como hoje o conhecemos. Enquanto o Lean reduz os desperdícios atuando em etapas que não agregam valor ao cliente, o Seis Sigma por excelência reduz a variabilidade das etapas que agregam valor.
A partir de 2012, o surgimento dos conceitos inerentes à Transformação Digital e o de tecnologias mais eficientes para armazenamento e compartilhamento de dados como a 5G, estão impulsionando o Lean Seis Sigma para um novo patamar. Essa evolução só aumenta a sua importância, visto que a tecnologia e abundância de dados sugere maior capacidade analítica para o método. Nesse sentido, data analytics, inteligência artificial, internet das coisas etc. têm sido associadas às ferramentas tradicionais estatísticas para obtenção de melhorias muitas vezes disruptivas em resposta às novas necessidades dos clientes e, consequentemente, dos processos. Assim, o Lean Seis Sigma pode e deve ser um aliado da humanidade para a obtenção dos pontos de inflexão levantados em 2015 e esperados para 2025 pelo Fórum Econômico Mundial como 5% de produtos aos consumidores impressos em 3D, e a consolidação das mudanças profundas como cidades inteligentes e armazenamento para todos, ambos retratados por Schwab.
Adicionalmente, essa nova era do Lean Seis Sigma conta ainda com a interação como Manifesto Agile de 2001, inicialmente aplicável a empresas de software e logo assumido pelas corporações em geral. Em seus 12 princípios, o Manifesto trouxe a base para a formalização de conceitos como o MVP (Produto Mínimo Viável) e o ciclo Aprender – Construir – Medir, explorado por Eric Ries , além de possibilitar a introdução de iniciativas e ferramentas para o desenvolvimento e a gestão de projetos como o Design Thinking, Design Sprint e o SCRUM .
Mas falemos um pouco de prática. Em 2011 iniciamos uma nova abordagem do Lean Seis Sigma na organização, centralizamos os treinamentos esparsos em iniciativas corporativas, inicialmente contando com consultorias e especialistas experientes, o que serviu para formarmos nossos primeiros Master Black Belt (profissionais formados e com experiência na execução de projetos e capacitação / multiplicação do método do Lean Seis Sigma).
Veja também
Ainda na abordagem tradicional, formamos as bases do programa cujo principal foco foi o desenvolvimento da cultura do pensamento científico na organização. Para isso precisávamos de massa crítica e rapidamente iniciamos o treinamento dos Yellow belts e Green belts, elaborando uma escola de formação que hoje inicia-se com o White belt na integração e chega até o Black belt. Não por acaso, com a consolidação dos métodos e da cultura atingimos ganhos expressivos nas fábricas e o treinamento contínuo possibilitou inclusive a criação da disciplina que nos permitiu manter tanto os treinamentos (logicamente que convertidos para formatos digitais) quanto a disciplina e a análise / execução dos projetos mesmo na época do Coronavírus.
Uma primeira evolução no programa sentimos com o incremento das tecnologias atreladas à transformação digital, algumas motivadas e comprovadas pelos próprios projetos Lean Seis Sigma. O método comprova a eficiência dos eventuais investimentos nas melhorias, sobretudo em sua fase quantitativa de Análise, que envolve geralmente comprovações das causas dos problemas com ferramentas estatísticas como testes de hipóteses, análise de variância (ANOVA), experimentos fatoriais e até simulação (twin digital) e análise de séries temporais de big data extraídos de sistemas e consolidados em BI, para citar alguns exemplos.
Quanto ao Agile, o Lean Seis Sigma o adotou inicialmente para acompanhamento dos projetos, com a utilização do kanban do SCRUM para acompanhamento do projeto em quadros nas áreas ou a partir de softwares gratuitos como o Trello, e iniciamos um método híbrido de algumas ferramentas que consolidamos no formato A3 para melhor visualização e acompanhamento.
Tivemos diversas experiências frustradas com treinamentos nos métodos Agile. Vendo todos saírem super-motivados e contagiados pelo treinamento, parecia que iniciaríamos um upgrade na nossa cultura para o método científico. Contudo, não conseguimos dar sequência nos projetos pois observamos que, após algumas semanas, o pessoal perde o ímpeto do treinamento e tudo começa a voltar ao normal e os projetos são deixados de lado em função de outras prioridades ou por falta de energia que requerem. Por experiência própria, nada melhor do que colocar um especialista de Lean Seis Sigma para acompanhar tais projetos. Eles garantem acompanhamentos mensais ou até semanais com as equipes para dar sequência e promover a mudança de cultura, iniciada com o treinamento. A partir dessa abordagem, mais de 70% dos projetos que são acompanhados de fato por um especialista com domínio dos conceitos de projeto e estatísticas, um blackbelt no Lean Seis Sigma por exemplo, chegam a um bom término com inovação e melhoria. Ao acompanhar e reportar o andamento, asseguramos o foco e mantemos o processo em andamento até que ocorra a desejada mudança na cultura organizacional. Desses resultados para incorporar os métodos no treinamento dos Green Belts é uma consequência imediata, e o Agile tem sido útil sobretudo nas etapas de Define (quando muitas vezes são necessárias novas abordagens para o problema) e Improve (na construção das soluções definitivas).
Como o leitor pode se assustar quando escrevo Define (a fase de definir do Lean Seis Sigma), cito uma experiência quando ao iniciarmos o projeto não tínhamos dados confiáveis e na quantidade necessária. Usamos o Design Sprint(*) que resultou na adoção de um controle com tecnologia da Indústria 4.0 para levantamento do histórico inicial do problema e continuação do método, que proporcionou melhorias em produtividade e qualidade no processo em estudo.
Na Universidade buscamos com o Seis Sigma a aproximação com consultorias, empresas de tecnologia e investimentos, por exemplo, de forma a permitir o compartilhamento de conteúdos específicos sobre como trabalhar as tecnologias da transformação digital. Também tecemos parcerias com outras Universidades, algumas fora do país, garantindo um foco extra e benchmarking com o que estão fazendo no resto do mundo.
Também realizamos parcerias com empresas para disponibilizarmos projetos complexos e reais na qualificação dos alunos. Essa abordagem permite que os estudantes tenham acesso a dados reais e ferramentas de última geração, gerando valor em análise e alcançando resultados para as empresas a partir da prática do método, devidamente assistidos por professores e por gestores das empresas. Assim, a execução de um projeto real por alunos nos últimos semestres de Engenharia de Produção, permite a eles formarem-se já com o título de Green Belt em Seis Sigma, o que certamente aumenta sua empregabilidade.
A aposta é que o Lean Seis Sigma é e continuará importante nas organizações que valorizam o pensamento científico e entendem que o caminho da melhoria é contínuo e necessário não só para a melhoria de produtividade, qualidade e atendimento de novas exigências do cliente, mas também como instrumento para a busca de atualização tecnológica e inovações disruptivas para o aumento da competitividade.
Alaercio Nicoletti Junior
Doutor em Engenharia de Produção e Master Black Belt em Lean Seis Sigma.
É o responsável pela Qualidade, Melhoria Contínua e Gestão da Inovação do Grupo Petrópolis
e atua como professor da Engenharia de Produção na Universidade Mackenzie
Siga-nos nas Redes Sociais