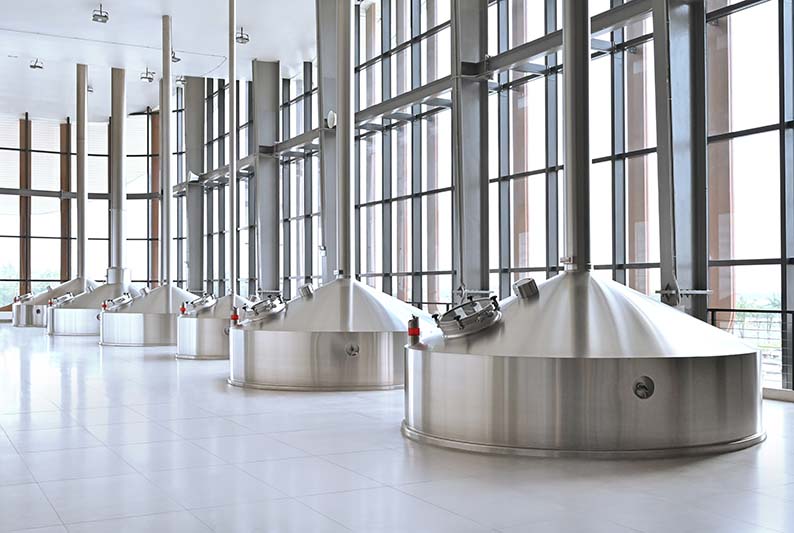
Os fabricantes de cerveja e bebidas precisam que a produção seja flexível,
consumindo poucos recursos e matérias-primas
A construção de novas plantas de produção impõe desafios crescentes para a indústria cervejeira e de bebidas. Não só as instalações têm de ser flexíveis e capazes de consumirem poucos recursos, como também as operadoras esperam que o tempo de comercialização seja o mais curto possível. Esses são apenas alguns dos fatores que a Ziemann Holvrieka considera ao desenvolver projetos turnkey, processo em que a empresa está comprometida com a padronização e digitalização.
No passado, na fase de concepção e desenvolvimento de um projeto, os engenheiros da planta trabalhavam em diferentes níveis para implementar os requisitos dos usuários. Além do processo produtivo em si, eram abordados os sistemas mecânico, elétrico e de automação, responsáveis por conectar todos os componentes do sistema. Para cada um desses níveis os gestores elaboravam um plano independente que exigia que os dados e informações necessários fossem coletados de diversas fontes ou coletados por meio do sistema de controle de processos. Mas este procedimento não era totalmente eficaz porque a deficiente definição das interfaces dos distintos setores faziam com que os sistemas não fossem compatíveis exigindo intervenção manual na programação tanto durante a fase de engenharia quanto no comissionamento.
“Plug and produce” graças aos MTPs
É justamente aí que entra o conceito de pacotes tipo módulo (MTP), uma ferramenta que vem sendo utilizada há anos com excelentes resultados na indústria química e farmacêutica e agora está sendo disponibilizada pela Ziemann Holvrieka para a indústria cervejeira e de bebidas em formato “open-source”. A ideia é tão simples quanto eficaz: os desenvolvedores fornecem módulos que podem ser integrados ao sistema de controle e reproduzem cada etapa do processo em detalhes. Dessa forma, o programador não precisa programar mais nada manualmente no local de instalação, basta simplesmente importar os dados.
O MTP contém todas as informações necessárias para cada fase do processo num formato normalizado, tais como dados relativos a Comunicação, as funções de engenharia de processos, uma descrição da interface homem-máquina (IHM) e informações de manutenção. Em outras palavras, os MTPs reúnem e vinculam todos os dados relevantes sobre o processo em si, os sistemas mecânico, elétrico, a automação e a manutenção para cada etapa do processo. Eles ainda cobrem componentes de campo como a válvula, bomba ou sensor. No caso de uma cervejaria por exemplo, os módulos seriam maceração, filtração e clarificação.
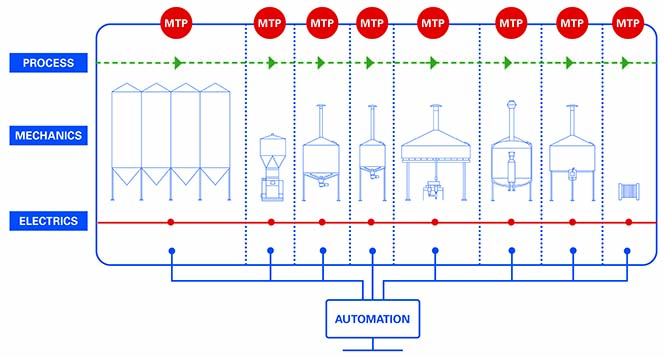
O método MTP é baseado em módulos que podem ser integrados ao sistema de controle e que reproduzem cada etapa do processo em detalhes
Todo o processo de fabricação de cerveja pode ser reproduzido com cerca de 25 MTPs no total. Assim, o construtor da planta pode projetar uma cervejaria composta principalmente de módulos ou seções e com capacidade para ser expandida. A grande vantagem é que qualquer sistema de controle compatível com um MTP fala a mesma linguagem do MTP, reduzindo o trabalho de integração no local, tornando todo o processo mais seguro e fácil. Graças a isso, é possível esquecer as dificuldades não previstas.
O MTP funciona de maneira semelhante a um Driver que conecta o computador a uma impressora de forma totalmente automática, permitindo que os dados sejam facilmente importados para um sistema de controle de nível superior para uso e visualização. Se uma nova planta de produção está sendo construída, os componentes podem ser integrados usando o conceito “plug and produce”.
Veja também
Menos trabalho durante o comissionamento
O processo de filtração é um bom exemplo de como o sistema funciona. Anteriormente, os técnicos precisavam primeiro instalar mecanicamente e ligar todos os componentes necessários, como a cuba de filtração e as bombas. O passo seguinte era a automação, que consistia em definir os pontos de conexão com os componentes instalados antes e depois e integrar todos os atuadores, sensores e etapas efetivas do processo, um a um, no sistema de controle. Este método manual implicava que uma parte do sistema final de controle de processos levava à empresa diferentes programadores, que em cada ocasião, se via quase que obrigado a reinventar a roda.
Com os MTPs, todas as informações relevantes do processo de filtração são coletadas antecipadamente em bancos de dados transversais, que atualmente contêm todo o conhecimento adquirido em mais de 50 anos de experiência na área de engenharia e automação cervejeira. A partir desses dados, um algoritmo gera o módulo de filtração adaptando-a às condições específicas da instalação. Tudo o que o programador no local precisa fazer é inserir esses dados no sistema de controle do processo, que visualiza automaticamente o processo de filtração, conecta todos os atuadores e sensores e executa as sequências.
Como resultado, os MTPs possibilitam padronizar ao máximo as descrições e automatizações dos processos, o que reduz consideravelmente a intervenção manual tanto na fase de engenharia quanto no comissionamento. Isto não só economiza tempo significativo, mas também limita a possibilidade de erros e reduz o trabalho necessário para o comissionamento em pelo menos 50%. E não é só isso: os MTPs fornecem ao usuário todos os dados e informações necessárias para modificar ou adicionar módulos a qualquer momento, mesmo quando o projeto está em sua fase inicial de planejamento.
Digital Twin para condições ideais
A Ziemann Holvrieka usa um gêmeo digital para dar vida virtualmente aos dados MTP. Este gêmeo é concebido como uma plataforma de dados baseada em nuvem que pode ser acessada, por exemplo, pelo usuário a partir de qualquer tablet convencional. Todos os dados MTP são armazenados na nuvem e podem ser facilmente recuperados. Além disso, o gêmeo possui ferramentas de visualização e algoritmos de simulação e análise.
Esse conceito oferece inúmeras vantagens como, por exemplo, permitir que o operador da planta faça um tour virtual pela futura cervejaria – tanto do processo quanto do sistema mecânico – desde o início da fase de planejamento. Dessa forma, o operador pode saber qual será o resultado muito antes da fábrica entrar em operação.
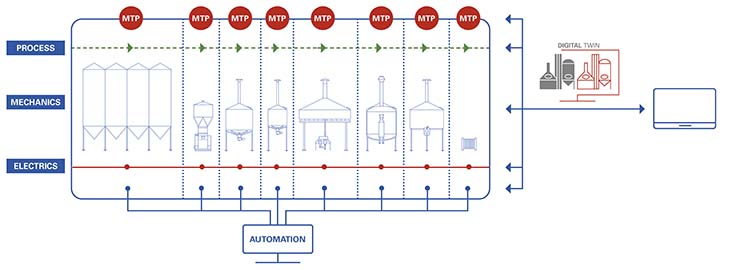
O gêmeo digital é uma plataforma de dados baseada em nuvem na qual todos os dados MTP são armazenados e podem ser recuperados
Os sensores também podem enviar para a nuvem em tempo real dados como, consumo, temperatura ou desempenho. Usando ferramentas de análise e algoritmos de última geração, o gêmeo digital utiliza esses dados para simular situações hipotéticas complexas com o objetivo de determinar as condições ideais de operação. Além disso, a identificação de tendências permite uma manutenção proativa. Por exemplo, o aumento constante no consumo de energia é uma indicação precoce de que uma das bombas tem um rolamento que não está funcionando corretamente.
Para que o intercâmbio de informações seja o mais seguro possível, a Ziemann Holvrieka aplica aos projetos cervejeiros as normas Weihenstephan, que definem uma interface de comunicação para a transmissão padronizada de dados de máquinas e processos para sistemas de TI de nível superior. Usando um módulo especial, os dados da nuvem podem ser exportados para qualquer solução de TI do cliente para processamento local. A Ziemann Holvrieka implementa projetos turnkey de última geração com MTP e gêmeos digitais em todo o mundo e as primeiras grandes instalações já foram concluídas com sucesso.
Créditos da imagem: Ziemann Holvrieka GmbH
Siga-nos nas Redes Sociais: