A unidade de Duque de Caxias da Coca-Cola Andina
é uma fábrica para quebrar paradigmas e se posicionar
entre as mais modernas e inovadoras da indústria mundial de bebidas
Carlos Donizete Parra | Fotos: Divulgação Coca-Cola Andina
Observamos nos últimos anos como a tecnologia e a transformação digital têm impactado nosso dia a dia. Nas indústrias, os níveis de automação e utilização de ferramentas digitais são cada vez mais elevados. A Coca-Cola Andina Brasil deu um grande exemplo de como é possível incorporar essas tecnologias em benefício do negócio e de seus consumidores. A empresa saiu na frente ao inaugurar a mais moderna fábrica da marca na América Latina, em Duque de Caxias, Região Metropolitana do Rio de Janeiro. A unidade é um modelo do mais puro conceito de Indústria 4.0, com monitoramento, geração de dados e automatização (100% dos equipamentos e processos digitalizados), aliando sustentabilidade, tecnologia e desenvolvimento econômico.
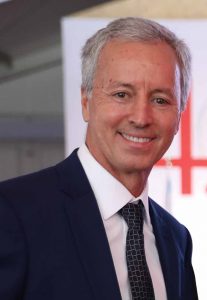
“Essa fábrica será uma referência para a indústria de bebidas”, Renato Barbosa, presidente da Coca-Cola Andina Brasil
A fábrica faz parte de um investimento de R$ 1,2 bilhão no Estado do Rio, que inclui ainda construção de um moderno Centro de Distribuição no Caju, na Zona Portuária do Rio, a modernização e ampliação de quatro outros Centros de Distribuição (Bangu, Nova Iguaçu, Campos e São Pedro da Aldeia), assim como adaptações e expansão da fábrica de Jacarepaguá, gerando 2.788 novos postos de trabalho.
“A inauguração da nova fábrica da Coca-Cola Andina é uma prova do compromisso da empresa com o Brasil e o Estado do Rio de Janeiro. É em Duque de Caxias que está instalada a mais inovadora unidade do grupo na América Latina. A instalação foi totalmente pensada e projetada para atender às necessidades mais específicas da operação, garantindo mais eficiência, segurança e qualidade para o consumidor. Essa fábrica será uma referência para a indústria de bebidas. Seguimos expandindo nossos negócios de forma sustentável, integrados ao meio ambiente e em sintonia com o desenvolvimento das pessoas e das comunidades em que estamos”, ressalta Renato Barbosa, presidente da Coca-Cola Andina Brasil.
“A inauguração desta fábrica inovadora é uma ótima notícia para a Coca-Cola Andina e o sistema Coca-Cola. Nossa estratégia está focada em atender às necessidades dos nossos clientes e consumidores locais. Com a nova unidade, Andina mais do que dobra sua capacidade de produção em garrafas retornáveis. Isso permitirá oferecermos embalagens sustentáveis e convenientes, contribuindo para o nosso compromisso de redução de resíduos. A nova fábrica ainda inclui um alto nível de tecnologia e usa energia limpa, além de contar com os mais altos padrões de qualidade. Parabenizamos a Coca-Cola Andina por este marco e agradecemos o investimento no futuro de nossos negócios”, afirma James Quincey, presidente da The Coca-Cola Company.
Novo conceito de produção
A KHS, referência mundial em equipamentos para produção e envase de bebidas, desenvolveu um novo conceito de fabricação de bebida com a nova minisala de xarope instalada na fábrica da Coca-Cola Andina Brasil, em Duque de Caxias. No processo tradicional de produção uma xaroparia distribui bebidas para todas as linhas de envase, enquanto neste novo conceito de minixaroparias dedicadas cada linha de produto pode ser considerada como uma unidade de fabricação. O projeto desenvolvido pela KHS traz como principais benefícios a redução dos riscos de contaminação, menos manutenção, além de tornar o processo muito mais ágil e flexível. “Além disso, foram reduzidos de forma considerável as perdas de produtos. A Coca-Cola Andina Brasil espera uma economia de energia ao redor de 30% e um aumento de cerca de 15% na disponibilidade do sistema”, explica William Wingeter, gerente de vendas de processos América do Sul da KHS Indústria de Máquinas Ltda.
Com a nova fábrica, a Andina é capaz de atender demandas futuras do Sistema Coca-Cola, ou seja, produzir diversos tipos de bebidas em uma mesma fábrica. Essa unidade já produz refrigerantes de vários sabores e água mineral em diversas embalagens e está preparada para fabricar sucos, isotônicos e outras bebidas não alcoólicas. O projeto foi concebido de acordo com os pilares da Indústria 4.0 e, principalmente com características de flexibilidade, sustentabilidade e eficiência operacional. A equipe de engenharia da Coca-Cola Andina Brasil trabalha neste projeto desde 2013, pesquisando alternativas tecnológicas e soluções de lay-out com o objetivo de obter os mais altos níveis globais de excelência operacional. Depois de diversas atualizações de projeto o resultado é fantástico, uma fábrica para quebrar paradigmas e se posicionar entre as mais modernas da indústria mundial de bebidas.
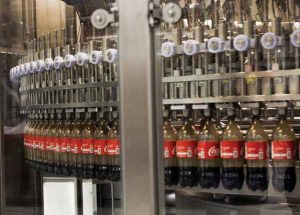
A Coca-Cola Andina Brasil
deu um grande exemplo de como é possível
incorporar essas tecnologias em benefício
do negócio e de seus consumidores
Projeto inovador
Sustentabilidade e inovação foram os pilares do projeto da nova unidade da Andina em Duque de Caxias. O layout da fábrica foi elaborado para ser flexível e expansível. Uma fábrica que pudesse permitir o fluxo de materiais, trânsito de veículos autônomos, ventilação e iluminação naturais, ambientalmente amigável, além de dispor das melhores tecnologias e de ser totalmente digitalizada.
Para receber todas as inovações propostas, o início foi literalmente pelo piso com acabamento impecável, feito a laser, com corredores amplos (cerca de 4 metros) permitindo a circulação dos LGV’s (veículos guiados a laser) de forma integrada com todas as áreas da empresa. A utilização de LGV’s possibilita a redução de custos com mão-de-obra e agiliza as operações de estocagem e distribuição de produtos acabados. Fabricados pela Elettric80 os LGV’s podem transportar de 2 a 4 paletes ao mesmo tempo, retirando os produtos da área produtiva, levando até a distribuição e de lá os paletes são encaminhados direto para os caminhões de entrega, sempre levando em consideração o FIFO, primeiro produto que entra é o primeiro produto que sai. Tudo feito de forma 100% automatizada, garantindo processos eficientes sem tempos de parada e espera de carregamento de caminhões, independente da quantidade de sku’s produzidos pela empresa.
Automação
A fábrica da Andina é uma referência para a indústria de bebidas, uma vez que utilizou o que existe de mais moderno em conceitos de fabricação, totalmente ligados aos pilares da indústria 4.0, como por exemplo xaroparias dedicadas por linha, processo de refrigeração inovador, entrada de insumos e saída de produtos acabados feito através de LGV’s, além de utilizar o sistema DanfossFlexConcept nos transportadores, tendo com isso controles mais precisos aliados ao benefício da eficiência energética.
A Danfoss do Brasil forneceu os conversores de frequência para vários processos da nova planta, para os mais diversos OEM´s e instaladores, por exemplo equipamentos para xaroparia e sopradora; nas linhas de envase, nos transportadores, e também para todo sistema de ar condicionado, onde controla as bombas e ventiladores.
Outra grande inovação da Coca-Cola Andina Brasil inédita no mundo está no abastecimento de insumos e matérias-primas. Essa operação é realizada exclusivamente por LGV’s, conferindo maior agilidade e controle ao processo. As informações dessas operações estão disponíveis em tempo real para possíveis ajustes e tomadas de decisão de todos os envolvidos. Os veículos autônomos podem trabalhar 24 horas sem nenhum tipo de emissão de carbono e contam com inteligência artificial para gerenciamento de estoque. Trabalham com bateria de lítio que podem ser carregadas automaticamente em uma estação própria sempre que necessário, sem interferir na rotina de trabalho.
Padrão mundial
A arquitetura inovadora da planta é responsável por uma eficiência energética inédita. A fábrica foi projetada dentro dos critérios do Green Building Council, com itens estruturais como telhados com isolamento térmico, sistema de drenagem pluvial mais eficiente, iluminação e ventilação naturais, recuperação de 100% da água do telhado. A iluminação artificial existente é 100% de LED e todo telhado é isolado termicamente reduzindo a necessidade de climatização dos ambientes. O teto das áreas é forrado proporcionando mais segurança aos processos produtivos e consequentemente ao produto final.
Este mesmo forro é caminhável e permite a realização de diversas operações de manutenção sem prejudicar a produção, além de evitar sujidades nas linhas, proporcionando segurança ao produto final. Os suportes dos mais de 600 pontos de iluminação foram desenhados segundo especificações da equipe de engenharia da Andina, permitindo trocas fáceis e rápidas por cima do forro.
Os laboratórios são integrados, o que não é normal em fábricas de bebidas, apesar de extremamente necessário. A nova unidade foi concebida com o objetivo de expansões futuras, mostrando claramente as expectativas otimistas da empresa com o mercado. “Estamos preparados para entrar em qualquer categoria de produto em questão de meses. Isso graças ao projeto e tecnologias que implementamos nessa nova unidade”, garante Rodrigo Klee, diretor industrial da Coca-Cola Andina Brasil.
Lavadora de garrafas sem o uso de vapor
As inovações implementadas geraram desafios a todos os envolvidos no projeto, principalmente aos fornecedores de equipamentos que tiveram que adaptar ou desenvolver soluções específicas às necessidades da Andina. A Liess, fornecedor tradicional do Sistema Coca-Cola, é um desses exemplos. A empresa desenvolveu uma lavadora de garrafas com aquecimento com água quente, sem uso de vapor, atendendo os padrões da nova fábrica que possui uma matriz energética inovadora e não utiliza vapor como meio de aquecimento. Além disso, a Lavadora Liess EcoLine conta com um exclusivo processo de gerenciamento da necessidade de água para o processo que garante um consumo máximo de 180 ml de água por garrafa lavada. As soluções da Lavadora Liess EcoLine estão totalmente integradas ao conceito da nova fábrica, com total otimização dos insumos e energia, garantindo consumos muito abaixo dos encontrados em máquinas similares. O nível de automação empregado também é um diferencial, com todo o processo controlado e monitorado de forma inteligente, exigindo mínima intervenção de operadores. O objetivo é eliminar variáveis do processo não controladas e garantir a melhor operação sob quaisquer condições, sempre com máxima eficiência e menor consumo.
Produção
A produção segue os pilares da Indústria 4.0 com processos digitalizados e tecnologias de ponta que posicionam essa fábrica como uma das mais modernas e inovadoras do mundo.
A sala de controle equipada com um videowall permite a visualização dos espaços e o acesso a dados e telas de todos os supervisórios da planta, assim como o monitoramento de todos os processos em tempo real, gerando alerta de eventos não desejáveis, sejam eles relacionados à produção, iluminação, ao ar-condicionado, à detecção de incêndio ou ao consumo de água, energia e utilidades em geral.
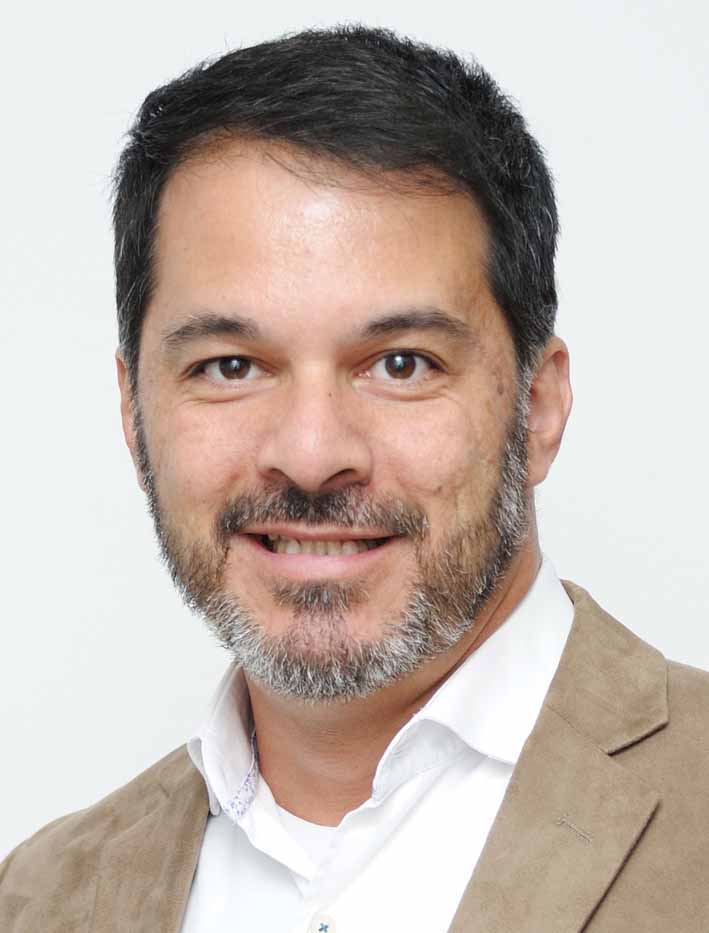
“O futuro mora na geração
de dados. Todas as soluções
dessa fábrica foram permeadas
e integradas pela digitalização”, Fausto Padrão, gerente
de engenharia da Coca-Cola
Andina Brasil
Todos os processos (linhas, utilidades, preparação de bebidas) e até mesmo sistemas prediais, estão constantemente gerando informações que são armazenadas no banco de dados em volume nunca praticado nas plantas do Sistema Coca-Cola.
Esta base de informação é o fundamento de todas as tecnologias envolvidas com o conceito da indústria 4.0. Sistemas como aprendizado de máquina (machine learning) e redes neurais (deep learning), por exemplo, só têm sua aplicação possível pela geração de dados completos que estão constantemente orientando os esforços de desenvolvimento. “O futuro mora na geração de dados. Todas as soluções dessa fábrica foram permeadas e integradas pela digitalização. Todo o sistema tem que gerar e entregar dados, a partir daí são integrados e se comunicam. Isso é distribuído para todas as áreas que necessitam dos dados, e as equipes podem prontamente tomar as decisões e ações pertinentes ao processo”, explica Fausto Padrão, gerente de engenharia da Coca-Cola Andina Brasil.
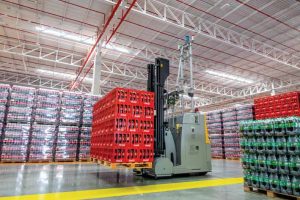
A arquitetura inovadora da planta é responsável por uma eficiência energética inédita
A fábrica tem capacidade para produzir 662 milhões de litros de bebidas por ano. Estão sendo produzidos no local refrigerantes (Coca-Cola, Coca-Cola Sem Açúcar, Fanta Laranja, Fanta Uva, Fanta Guaraná) e água mineral com e sem gás, em diferentes tipos de embalagens. A nova unidade também permitirá à empresa duplicar sua produção em PET retornável. A Andina é o terceiro maior fabricante do Sistema Coca-Cola no Brasil com cerca de 12% de market share.” Apesar da crise, tanto nós da Andina como o Sistema Coca-Cola em geral ganhou market share. Com os investimentos nessa fábrica estamos preparados para o aumento de consumo que deve começar a ocorrer em breve. Estamos em condições competitivas para atender prontamente o mercado”, explica Fernando Fragata, diretor jurídico e de relações institucionais da Coca-Cola Andina Brasil.
Sistema de refrigeração descentralizado
A Frigel forneceu a solução de refrigeração e aquecimento para o processo, compatibilizando as necessidades de frio e calor e utilizando sistemas de refrigeração inteligentes, possibilitando a recuperação de calor dos equipamentos de refrigeração, através de bombas de calor, diretamente no processo com sistemas individualizados por linha de produção garantindo máxima precisão e estabilidade. Os sistemas reduziram o consumo energético total da planta, nestes processos, em cerca de 30%. Outro grande diferencial é utilizar um sistema100% livre de amônia garantindo o máximo de segurança para a operação.
“Com certeza, o projeto desta nova fábrica foi concebido visando eficiência, sustentabilidade e segurança operacional com toda modelagem da indústria 4.0. Todos os equipamentos da Frigel estão plenamente integrados a este conceito. Nosso projeto tem funcionamento praticamente autônomo e é gerenciado totalmente no centro de controle da planta. Esta fábrica servirá de modelo a muitas indústrias pois os conceitos e tecnologias empregados em todo o processo e movimentação logística extrapolam a indústria de bebidas”, Maurício Beduschi, diretor comercial da Frigel Latino América.
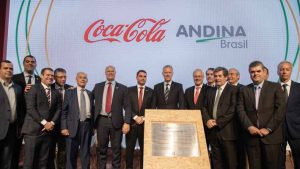
Executivos globais da companhia e autoridades participaram da cerimônia de inauguração.
Entre os presentes estavam o presidente mundial da Coca-Cola Company. James Quincey,
o presidente do Diretório da Coca-Cola Andina, Juan Claro González, o vice-presidente executivo da Coca-Cola Andina, Miguel Angel Peirano e o presidente da Coca-Cola Brasil, Henrique Braun
A inovação pode ser encontrada em todas as áreas da fábrica, como nas mini-xaroparias dedicadas a cada linha de produção, nas salas de CIP (preparo de fluidos de limpeza) e no sistema de refrigeração, todos independentes por linha ou descentralizados.
Veja também
“Normalmente, se tem uma grande xaroparia que distribui bebidas para todas as linhas de envase. A Coca-Cola Andina descentralizou isso e toda linha tem sua xaroparia dedicada, transformando cada linha em uma pequena unidade de fabricação”, explica Fausto Padrão.
As mini-xaroparias dedicadas foram fabricadas pela KHS, multinacional alemã e uma das principais fabricantes globais de equipamentos para bebidas. Elas trazem benefícios como: redução dos riscos de contaminação, menos manutenção, mais flexibilidade e agilidade. Tudo isso com uma operação simplificada e com tempos menores de processo. “Existe muita sinergia entre o operador da xaroparia e o processo de fabricação da bebida, contribuindo ainda mais para o aumento da eficiência dessa área de produção”, esclarece Fausto Padrão.
Esse modelo utilizado na fabricação de bebidas é altamente eficaz contra contaminações e acidentes, com linhas e fluxos independentes. Ele foi replicado com o mesmo conceito nas linhas de CIP, também independentes, apresentando vantagens em relação ao sistema tradicional como a redução de custos com energia e mão-de-obra, além de eliminar tempos de espera mostrando ser um modelo que apresenta sinergia e ganhos operacionais à fábrica como um todo.
Envase
Na área de envase, a utilização de linhas de produção com tecnologia triblock é inédita no Brasil, ou seja, todo o processo, desde a fabricação da garrafa, rotulagem, enchimento e colocação da tampa é feito numa mesma máquina. O sistema Ergobloc L, fabricado pela Krones, empresa líder mundial na produção de equipamentos para fabricação e envase de bebidas,tem capacidade para 37 mil garrafas de PET por hora de 2 litros e apresenta benefícios como redução do espaço ocupado (área até 30% menor comparada com blocos convencionais e até 70% menor comparada às linhas convencionais com utilização de transportadores de garrafas); não possui transportadores e sistemas de acúmulo (pulmão) entre um equipamento e outro, que reduz incidência de mau funcionamento, gera maior eficiência que a utilização de equipamentos separados; redução de CAPEX e custos com manutenção, trazendo mais segurança ao produto final. O equipamento requer menos mão-de-obra e proporciona uma operação ergonômica do bloco com um operador, além de consumir menos energia elétrica.
Inteligência no centro de tudo
Graças à utilização de tecnologias inovadoras e através da análise dos processos logísticos dos clientes, Elettric80 e BEMA anteciparam, já há 25 anos, o conceito de Indústria 4.0: a fábrica inteligente, interconectada e digitalizada.
A Coca-Cola Andina Brasil, instalada em Duque de Caxias, é um exemplo desse conceito que põe a inteligência no centro de tudo e não a máquina.“Especialmente onde grandes volumes são movimentados, seja matéria-prima, seja o produto final, explica Enrico Grassi, presidente da Elettric80 e BEMA, nossa intervenção garante retornos significativos em termos de eficiência e, conseqüentemente, de margens”.
“Juntamente com a direção da Coca-Cola Andina, diz Luca Guidetti, presidente da filial da Elettric80 e BEMA na América Latina, desde 2015 projetamos e implementamos de modo personalizado o layout dessa fábrica avançadaa fim de gerenciar toda a atividade e assegurar a total rastreabilidade dos produtos movimentados”.
Um exemplo disso são as operações logísticas, gerenciadas por meio de soluções automatizadas e integradas da Elettric80 e BEMA. Veículos automáticos guiados a laser (LGVs), sistemas de controle de paletes, envolvedoras robotizadas de alta velocidade, armazéns para a estocagem de matérias-primas e de produtos acabados; tudo diretamente da plataforma de software SM.I.LE80.
Além do ERGOBLOC L, a Krones forneceu outros equipamentos que compõe a linha, como embaladora de filme termoencolhível, paletização e os sistemas de transportadores de garrafas, pacotes e paletes e os equipamentos de inspeção.
Destaque também para utilização de um warmer, Krones Linatherm, que elimina a condensação na parede das garrafas, molhando o palete de produto, premissa para o correto funcionamento dos LGV’s. Além disso, esse equipamento opera com o reaproveitamento da energia térmica utilizada no processo de refrigeração das bebidas, o que contribui com a eficiência energética da fábrica. Outras soluções de economia de utilidades e energia foram aplicadas em outras máquinas da linha, individualmente, seguindo os mais atuais conceitos de sustentabilidade, como reaproveitamento de calor do warmer, reaproveitamento de ar de sopro, sistemas de economia de energia do forno da embaladora, entre outros.
A linha de água mineral Crystal possui a mesma tecnologia usada na linha CSD, um ERGOBLOC L com capacidade para 32.000 garrafas/hora de PET de 500 ml sem gás.
A terceira linha também foi fornecida pela Krones e trabalha com garrafas REFPET de 2 litros com capacidade para 24.000 garrafas por hora.
Destaque para o inspetor com tecnologia de espectrometria de massa, para eliminação de garrafas contaminadas não passíveis de lavagem, além da rotuladora de princípio construtivo modular, que atende às novas estratégias da Coca-Cola com relação à otimização de SKUs e à flexibilidade que permite a rotulagem em linha das garrafas retornáveis.
Automação industrial
No controle dos processos de envase e xaroparia de refrigerantes, a Coca-Cola utiliza tecnologia da Siemens com a linha SIMATIC, como IHMs (interface homem-máquina), controladores e equipamentos de infraestrutura de redes de comunicação. Já nas estações de tratamento e saneamento foi implementado o SIMATIC WinCC para o controle, supervisão e aquisição de dados do processo (SCADA).
Nos centros de estoque e distribuição da Coca-Cola, toda a infraestrutura de rede Wireless que suporta a comunicação dos LGVs foi instalada usando switches da linha SCALANCE, controladores SIMATIC e IOs distribuídos da Siemens.
Essas soluções foram desenvolvidas na plataforma TIA Portal, o que permite que a Coca-Cola faça toda manutenção dos sistemas de LGVs, redes de comunicação, controladores e supervisório a partir de uma única ferramenta de engenharia.
Essa característica pode ser traduzida em processos simplificados, mais agilidade e autonomia, redução dos custos de operação e menor time to market dos produtos
Digitalização
A unidade da Coca-Cola Andina Brasil possui 100% dos equipamentos e processos digitalizados, aliando sustentabilidade, tecnologia e desenvolvimento econômico.
Conta com monitoramento online dos dados operacionais, plataformas de Internet das Coisas (IoT), e está preparada para soluções de realidade aumentada, Inteligência Artificial e Big Data. De acordo com Renato Barbosa, o nível de automação e digitalização dos dados alcançados garantem mais agilidade, controle, segurança e eficiência.
A fábrica possui quatro redes de comunicação distintas para evitar conflitos de endereço e saturação de bandas. Essas redes compõe o data center da fábrica (redes de TI, TA, CFTV e de subestações elétricas), sempre operando separadamente. Todos os sistemas estão integrados e funcionando perfeitamente, garantindo segurança dos dados e informações, além de evitar interrupções da fábrica.
Sustentabilidade
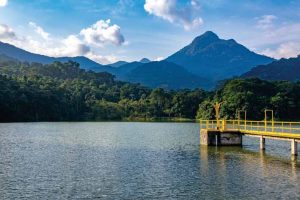
A sustentabilidade é um, dos pilares
da nova fábrica. Na área destinada à
sua construção, a empresa promoveu
um processo de recuperação ambiental
no qual foram investidos mais
de R$ 20 milhões
A sustentabilidade é um dos pilares da nova fábrica, a terceira da Coca-Cola Andina no país – as outras ficam em Jacarepaguá (RJ) e Ribeirão Preto (SP). Na área destinada à sua construção, a empresa promoveu um processo de recuperação ambiental no qual foram investidos mais de R$ 20 milhões. Dentre as iniciativas realizadas estão a revitalização do terreno e da represa localizada no terreno, o monitoramento da fauna e flora local e o replantio de 3.800 espécies nativas da região. Também foi criada uma área de preservação ambiental de 31,2 hectares, o equivalente a mais de 30 campos de futebol e implementados 13 programas de educação ambiental na comunidade do entorno.
Modernidade e rapidez no envase
Alinha de envase de refrigerantes e água da nova fábrica da Coca-Cola Andina representa o que há de mais moderno e mais rápido no mundo.
A linha de refrigerante é a maior do mundo (37.000 garrafas por hora para 2 litros – Coca-Cola) e da mais alta tecnologia, usando, além disso, o conceito ERGOBLOC L (combinação de várias máquinas blocadas: sopradora, rotuladora, enchedora e tampadora). “Além de tudo isso, o que nos motiva é que esse é o primeiro ERGOBLOC L instalado no Brasil e, de uma só vez, instalamos dois na mesma planta (1 para refrigerante e outro para produção de água mineral)”, comemora Silvio Rotta, diretor comercial da Krones.
Tribloco é o termo popularmente usado para esse conjunto de equipamentos, mas a Krones reconhece para esse tipo de combinação de máquinas o ERGOBLOC L, pois segundo a empresa não se trata apenas de conectar ou juntar 3 máquinas.
O termo ERGO vai muito além, pois vem de Ergonomia, em que uma só pessoa pode operar todas as máquinas. Além disso,o sistema propicia uma atuação muito mais eficiente e a vista da linha como um todo.
“Se voltarmos há 10 anos, uma linha de refrigerante de 24.000 garrafas por hora existente em muitas fábricas(era uma linha considerada de grande volume para a época), era composta praticamente por seis equipamentos a mais para fazer o mesmo trabalho de um ERGOBLOC L, com muito mais operadores, maior custo de energia, ocupando muito mais espaço e com mais manutenção, sendo que também devemos levar em conta a diferença de produção (37.000 gph x 24.000 gph).
Ou seja, o custo total do produto, produzido em uma linha ERGO, tende a ser muito menor se comparado com linhas convencionais ou mesmo em bloco sopradora, enchedora e tampadora”, finaliza Silvio Rotta.
Esta é também a primeira fábrica de Coca-Cola no Brasil que não utiliza caldeiras como fonte de energia térmica em seus processos, e sim água quente, e nem amônia na refrigeração. O gás refrigerante utilizado é o R 513, um gás totalmente ecológico, não prejudicial ao meio ambiente e que evita a degradação da camada de ozônio.
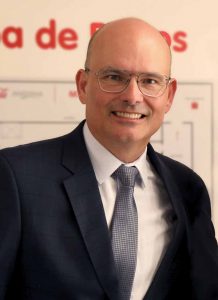
“Estamos preparados para entrar em qualquer categoria de produto em questão de meses graças
ao projeto e tecnologias que implementamos na nova unidade”, Rodrigo Klee, diretor industrial
da Coca-Cola Andina Brasil
Sem vapor no sistema, a água quente é aquecida e estocada para ser utilizada em todos os equipamentos de acordo com dois níveis de temperaturas: 75oC (lavadora e warmer) e 90oC (CIP), gerando mais segurança e economia de energia. “Todo o processo de produção foi desenhado para operar com uma economia de 20% em energia e de 30% em água em relação à média do sistema Coca-Cola no Brasil”, garante Rodrigo Klee, diretor industrial da Coca-Cola Andina Brasil.
Também foram construídas Estação de Tratamento de Água (ETA) e Estação de Tratamento de Efluentes (ETE) com monitoramento e controle automatizados. No caso da ETE, foram implantadas redes de efluentes segregadas. Todos os descartes/efluentes são enviados a Estação de Tratamento por cinco redes de efluentes diferentes e recebidas em tanques separados. A partir daí os efluentes são gerenciados pela ETE de acordo com as características dos fluidos coletados. Isso gera menos problemas à ETE e muito mais eficiência ao sistema. As tubulações utilizadas na fábrica também tiveram uma atenção especial. Foram utilizadas tubulações de vários tipos de plásticos, menos sujeitos à degradação por ação dos efluentes, pensando em possíveis vazamentos e complicadas manutenções que possam futuramente comprometer o funcionamento da unidade ou degradação do solo.
De acordo com Fausto Padrão, as subestações elétricas são outro destaque, pois utilizam o conceito de “eletrocentros” – unidades pré-montadas em contêineres. O sistema agilizou o tempo de montagem, além de gerar mais segurança na utilização de energia e facilitar a manutenção, também já está preparado para ampliações futuras da empresa.
“Estamos há 25 anos no Brasil e escolhemos o Rio de Janeiro como base de nossas operações no território brasileiro. Esta fábrica reafirma a nossa crença num ambiente de trabalho capaz de atrair, desenvolver e reter os melhores talentos disponíveis. Nos enche de especial orgulho o processo de recuperação ambiental que promovemos no terreno, onde criamos uma área de preservação ambiental permanente de mais de 31 hectares, promovemos um reflorestamento com mais de 3.800 mudas de espécies nativas da Mata Atlântica e criamos um programa de monitoramento de flora e fauna, além da construção da fábrica de acordo com os critérios exigidos para a obtenção da certificação LEED”, finaliza o vice-presidente executivo da Coca-Cola Andina, Miguel Ángel Peirano.